Licensing MagnaFlo® Technology
Just of Few of the Reasons to Consider a MagnaFlo® Technology License
Images of Paraffin Problems Found in Field Operations
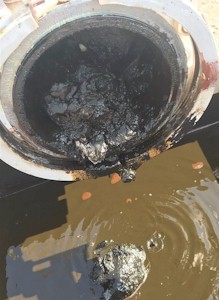
Huge Reoccurring Problems to Address
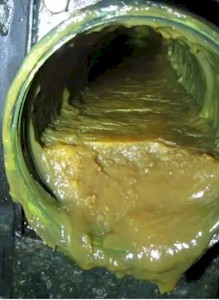
Clogged Pipes
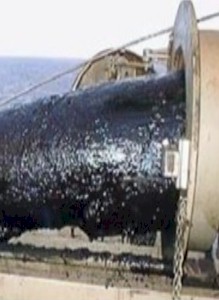
Too Much Down Time
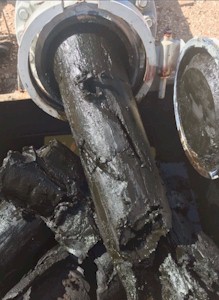
Big Clean Outs Requiring Many Hours of Labor
MagnaFlo® Service Licensing Opportunities are Currently Available for US and Overseas Markets
Pipeline Paraffin Problems
The world demand for energy has led oil companies to expand their operations and production to produce more oil and gas even when the environment presents problems such as cold temperatures causing the paraffin buildup problems in both down hole environments and in transportation lines feeding from reservoirs to the sales markets. This problem can also cause issues in offshore production due to water temperatures become colder and colder the deeper you go.
During hydrocarbon production, oil companies are challenged with the problem of paraffin deposition from the crude oil building up on the pipe wall. The precipitated solid phase of paraffin, creating pressure abnormalities and causes an artificial blockage leading to a reduction or interruption in the production. It leads to increases in operational and remedial costs while suppressing oil production. This underscores the importance of using MagnaFlo® over other methods that are currently being used to reduce or mitigate paraffin deposition in the hydrocarbon production systems around the world. Our pilot projects confirmed the validity of using MagnaFlo® products in leu of other methods and chemistries currently being used to mitigate the paraffin issues found in crude oil. Many service operators have used various different types of chemical inhibitors. The reduction in paraffin deposition was realized but only after creating more work or problems brought on by the use of those methods and chemical inhibitors. Despite of all the previous mitigation methods, many oil companies still suffer from paraffin deposition problems and are still looking for a good solution to solve this issue. It was for this purpose, MagnaFlo® was developed. A mitigation product environmentally sensitive that causes the paraffin molecules to separate and loose its attraction to recongeal which has no extended effects once the oil has made it to market and has been placed in a refining environment.
Paraffin deposition is one of the main flow assurance problems faced by the oil industry, affecting numerous oil companies around the world. Paraffin deposition can result in the restriction of crude oil flow in the pipeline, creating pressure abnormalities and causing an artificial blockage leading to a reduction or interruption in the production (Figure 1). The main causes of paraffin deposition are environmental changes, including temperature, pressure, and loss of dissolved gases, which affecting solution equilibrium, therefore pressure abnormalities are formed due to evaporated the dissolved gases (light components of the oil) from the crude oil. This pressure abnormality which means principally overpressure or under pressure will affects production capacity, wellhead oil pressure dropped significantly and faults in the separation facilities. However, in an extreme case, this can cause a pipeline or production facility to be abandoned. The paraffin deposition also leads to formation damage near the wellbore, reduction in permeability, changes in the reservoir fluid composition and fluid rheology due to phase separation as paraffin solid precipitates.
One of the important issues to be noted is that the paraffin deposits are not solid paraffin, but a gel that consists of solid paraffin crystals and trapped liquid. The deposit is also known to harden with time in a process termed aging. The precipitation of paraffin components out of the oil is responsible for changes in the paraffiny crude oil properties, including the gelation of oil and an increase in viscosity. Paraffin contains a high molecular weight and consists of long chain alkanes with 20 to 50 carbon atoms. Paraffin can precipitate as a solid phase when the crude oil temperature drops below the paraffin appearance temperature WAT (the temperature at which the first paraffin crystals start to form in the crude oil in a cooling process).
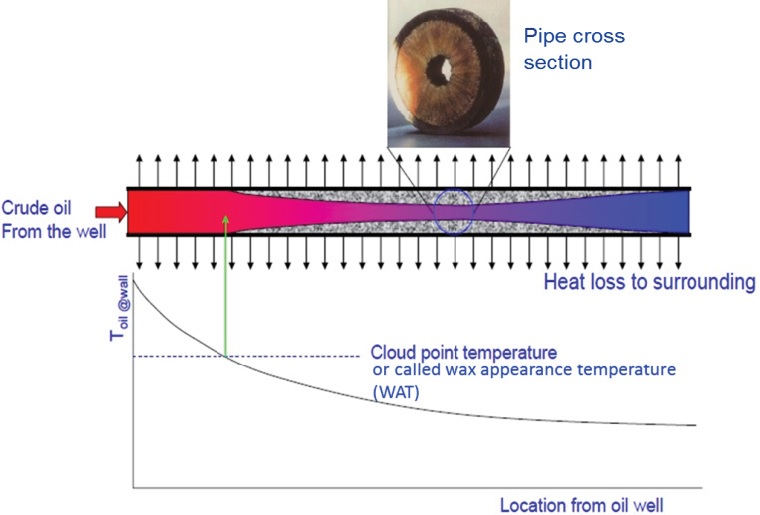
Figure 1: Paraffin deposition process in the hydrocarbon
The main factor that affects the paraffin deposition process is the low temperature, which means that subsea pipelines are especially vulnerable. Therefore, paraffin deposition prevention becomes very important in deep-water oil production. Paraffin deposition in crude oil production systems can be reduced or prevented by one or combination of chemical, mechanical, and thermal remediation methods. However, with the advent of extremely deep production, offshore drilling and ocean floor completions, the use mechanical and thermal remediation methods becomes prohibitive economically, as a result, use of chemical additives, such as MagnaFlo®, as paraffin deposition inhibitors is becoming more prevalent.
The thermal methods include heat retention, active heating such as thermal insulations, bottom hole heaters, hot oil circulation and steam circulation. The mechanical removal method includes running scrappers in the borehole and pigging in pipelines at an intervention frequency. All vary labor intensive and all with side effects to the oil.
The chemical inhibitors include pour point depressants, crystal modifiers, dispersants and solvents. Also, there are other mitigation methods such as, microbial treatment using microorganisms for paraffin mitigation, cold flow, cold-oil recirculation method, choke cooling method, the paraffin eater method, magnetic fluid conditioning method, Eco-wave TM treatment, ultrasonic wave treatment, bacterial treatment, and spiral flow method. Most too costly to benefit the producer.
Despite of all of those mitigation methods, many oil companies are beginning to prefer chemical inhibitors in cold environments, considering this economic way and best solution to reduce paraffin deposition in pipelines due to chemical additives does not need to stop production for cleaning the pipe but it considers as an online mitigation method.
The Solution
MagnaFlo® technologies are a hands-off self-contained treatment technology that only requires periodic maintenance, several checks per month as opposed to the other mentioned methods for treatment.
MagnaFlo® Paraffin mitigation process
This process utilizes a combination of the MagnaFlo® paraffin mitigation technology in association with historically accepted mechanical methods to mitigate the paraffin problems found in pipeline transportation collection facilities.
Mechanical Removal Method Used
Mechanical-removal
Techniques and methods are the oldest paraffin-removal techniques applied in the industry. The following mechanical-removal method is used to remove paraffin deposits from flow lines and pipelines: pigging flow lines.
Use of pipeline-inspection gauges (PIGs) is a mechanical method that is the oldest and among the most widely used paraffin-removal techniques in the field.
PIGs have been used in the petroleum industry for more than a century, and there are arguments that suggest the acronym (PIG) may also have been derived from the squealing noise they make while traveling through a pipeline. A PIG is launched from a PIG launcher, which is a section of the pipeline with a larger diameter gradually reducing to the normal diameter of the pipeline. As the PIG is launched, the launching station is closed and the pressure driven flow of the hydrocarbon in the pipeline pushes the PIG through to the receiving center. The PIG while traveling can scrape off the paraffin deposits from the pipeline walls. Figure 2 shows how a cleaning PIG can operate within a section of pipeline.
Frequency of the cutting and pigging (to remove depositions in flowlines) depends on the paraffin deposition rate in an individual pipeline.
The improved flow due to the passing pig is probably caused by a combination of smoothing of the rough paraffin layer and removal of the paraffin back into the flowing well. The pig selection depends on paraffin properties operating parameters. However, a maximum paraffin layer thickness of 2-3 mm is often used as pigging criterion.
What Describes a MagnaFlo® Client
Any pipeline requiring pigging for than twice a month is an economic candidate for the MagnaFlo® paraffin mitigation process. The MagnaFlo® process, although being economical, one major advantage found is plugging of perforations within wells as a result of circulation of scraped paraffin through the well annulus does not occur. The MagnaFlo® technology will not allow the paraffin molecule to reform into a clot or mass causing blockages or stoppages. Efficient utilization of pigging in combination with the MagnaFlo® technology allows the operator to maintain a predictable delivery system of product to market. The scraping damages a pipeline receives by pigging or scraping also decreases its productive life. MagnaFlo® in concert with periodic mechanical treatment will increase the performance of the pipeline and increase the stability of oil-in-water emulsions.
Another advantage of the mechanical method in combination with the MagnaFlo® technologies includes good thorough cleaning is assured with minimal or no pipeline damage. Also, some other advantages of using the MagnaFlo® technologies with PIGs include low labor costs, simplicity of operation, and less downtime because cleaning will be faster.
MagnaFlo® Chemical inhibitor
MagnaFlo® technology inhibitors are considered as the best solution for hydrocarbon production. The MagnaFlo® chemical inhibitor breaks the bonds between the oil molecule and the paraffin molecule. Once broken, MagnaFlo® will not allow the paraffin to reabsorb into the oil. This feature has been tested over in multiple lab settings for the past twenty years. Although all these factors are at work in the oil, none
MagnaFlo® Service Licensing Opportunities are Currently Available in the US and Overseas Markets
If you own or operate an oil and gas service company and have interest in obtaining a MagnaFlo® Technologies Service License, Please complete the form below and a MagnaFlo representative will contact you shortly.
United States License Request
Foreign License Request